The industrial landscape is rapidly evolving as intelligence and advanced technologies take center stage in 2024. Specifically, automated material handling systems (AMHS) are growing in popularity and expanding their presence across numerous sectors from manufacturing to construction. In this article, we’ve put together a comprehensive guide to help you understand everything you need to know about the future of AMHS.
Globally, industries are implementing these systems at every stage to improve efficiency, safety, and labor shortages, optimizing operations like never before. This aligns with the broader trends of smart manufacturing, 4IR (Fourth Industrial Revolution), and Industry 4.0, highlighting the growing significance of integrating cutting-edge technologies in the industrial sector.
With a wider adoption of automated material handling systems comes substantial market growth. In fact, according to Mordor Intelligence, the AMHS market is set to reach $70.35 billion in 2024 and is additionally projected to grow to $126.20 billion by 2029. These projections alone are one key indicator of the growing popularity of AMHS.
In this guide, we’ll take a closer look at some of the key trends we're seeing emerge within AMHS, the different principles of material handling, and their various applications across several different industries.
8 Trends in Material Handling Automation for 2024
1. Increased Data Collection and Analysis
The first key trend following material handling automation in 2024 is increased data collection and analysis, which is emerging as a driving force behind informed decision making. Automation systems are becoming robust data generators, helping organizations to learn, adapt, and optimize operations.
At Cyngn, our technology helps organizations aggregate data about vehicles to extract business insights and help improve operations through tracking key metrics such as battery life, location, and cycle time. Having such data available can help organizations respond to potential issues down the line and pivot operations when needed.
Cyngn also provides insights on vehicle productivity, identifying opportunities for optimization and cost savings. Together, this data contributes to better decision making and the ability to respond to changing demand.
2. Expanded Use of AI
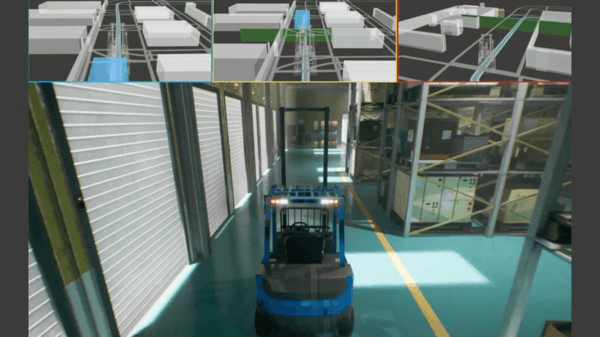
According to McKinsey's 2022 AI Survey, AI adoption has more than doubled since 2017, and the average number of AI capabilities that organizations use has drastically increased by 50% since 2018.
In material handling, AI is being used to make better decisions, predict maintenance needs, and optimize operations. Combining AI with IIoT technologies can help organizations improve overall cost-effectiveness and adaptability.
In particular, artificial intelligence has significantly influenced the development of industrial autonomous vehicles. As a result, robotics and automation will account for more than 25% of capital spending over the next five years for industrial companies, according to the 2022 McKinsey Global Industrial Robotics survey.
When it comes to Cyngn’s technology, we have leveraged advancements in AI to enhance our Enterprise Autonomy Suite (EAS). We use learning-based approaches for computer vision to analyze, interpret, and understand sensor data, including deep learning and machine learning (ML) models that can learn and improve from experience.
3. Implementation of IIoT (Industrial Internet of Things)
IIoT integrates smart devices and sensors, allowing material handling to become more adaptive and connected. As a result, industrial equipment and machinery have become seamlessly interconnected. This leads to a network where data is not only collected but it is also shared intelligently across the entire ecosystem.
4. Addressing Cybersecurity Risks
With increased intelligence and data comes potential threats. To combat these cybersecurity threats, companies are increasingly incorporating preventative measures and authentication protocols to help monitor, detect, and respond to these risks in real-time. By addressing cybersecurity risks, businesses can ensure the security and the optimal functionality of material handling systems.
5. Predictive Maintenance and Optimization
Organizations are also embracing predictive maintenance in 2024. By leveraging analytics, businesses are now able to anticipate equipment failures before they occur. This allows for timely interventions and reduces unexpected downtime, ensuring that material handling systems operate at peak performance levels.
6. Managing Worker Shortages
According to the US Chamber of Commerce, there are currently 9.5 million job openings with only 6.5 million unemployed workers, leaving a huge gap to be filled.
As a result, material handling robots have risen as a key solution to tackling the issue head-on. By taking on repetitive tasks and transport routes, industrial robots can free up an estimated 30-50% of a skilled worker’s time. In doing so, companies can increase their production with fewer employees and at the same time assign their workers to more valuable tasks.
In fact, when Cyngn deployed one of our autonomous vehicles at GLF's Las Vegas warehouse facility, it led to a dramatic decrease in labor costs— almost immediately. We found a 64% reduction in labor costs when our autonomous stock chaser was deployed instead of a manual forklift.
7. Energy-Efficient Solutions
According to a survey conducted in 2022 by the National Association of Manufacturers, 68% of executives plan to implement extensive, corporate-wide sustainability strategies. This number has risen from just 39% in 2019.
Automated solutions, from energy-efficient conveyor belts to robotic systems, are key to minimizing environmental impact and optimizing operational costs. Plus, as environmental regulations become more stringent, the adoption of these solutions help businesses comply with regulations and demonstrate a commitment to long-term sustainable practices.
8. Use of Swarm Robotics
Inspired by the work of social insects, swarm robotics are groups of robots that work together. Each robot follows simple rules, communicates with its peers, and collaboratively adapts to the environment. This allows them to efficiently execute tasks by responding to changing conditions and demands in a coordinated manner, something that is important in material handling automation.
Types of Material Handling Equipment
Engineering Systems
Engineered systems are the foundation of modern material handling. In material handling, these systems integrate various technologies to streamline and automate the movement, storage, and control of materials within industrial settings.
Examples include AGVs, AS/RS, AMRs, and other specialized industrial vehicles, each uniquely designed to complete industrial tasks. Let’s explore each in more detail.
AGVs
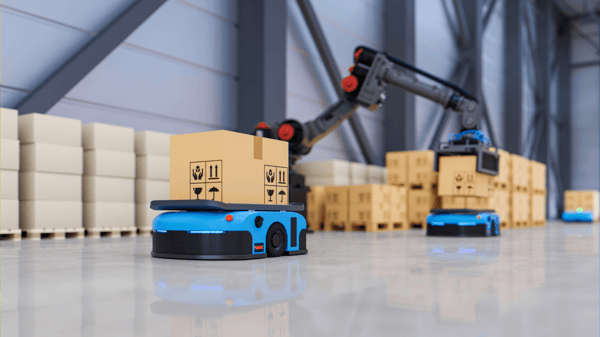
Automated guided vehicles (AGVs) play a pivotal role in material handling automation and are important to automating movement across structured environments. These intelligent, driverless vehicles navigate predetermined routes within a facility using embedded guidance systems such as lasers, magnets, and vision systems. You can think of AGVs similar to how a train follows a predetermined track.
AGVs tend to involve tasks that require the repetitive, safe, and efficient delivery of goods, such as material transportation, pallet handling, and order picking. While AGVs operate efficiently in simple loops, they can stall out if the route gets obstructed and therefore are best for simple use cases.
AS/RS
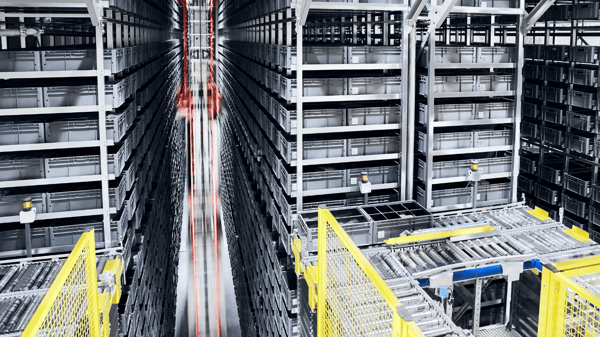
Automated storage and retrieval systems (ASRS) replace large storage areas with vertical storage spaces, transforming the conventional approach to storing and retrieving materials within a warehouse. AS/RS systems combine automation with strategic planning to automatically place, store, and retrieve product or inventory on demand. This ensures swift access to goods while saving floor space by increasing inventory storage density.
Some examples of AS/RS include carousels, mini-load, unit load, cranes, and shuttles that replace large storage areas and save floor space. By optimizing vertical storage space and enhancing retrieval speed, AS/RS contribute to increased efficiency and reduced operational costs.
AMRs
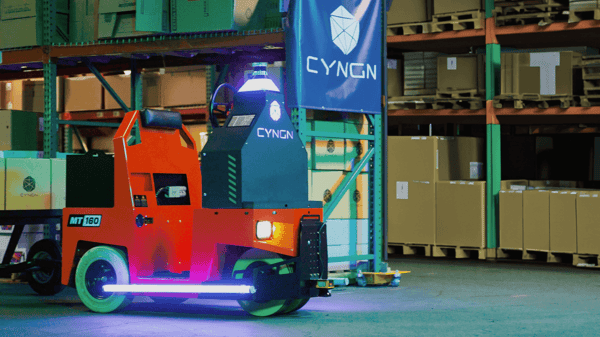
Automated mobile robots (AMRs) use advanced technology such as artificial intelligence, machine learning, sensors, and path planning to autonomously navigate without direct human oversight. In comparison to AGVs and AS/RS systems, these vehicles can intelligently navigate without a fixed route and do not need to adhere to the fixed infrastructure of a storage structure.
As a result, AMRs greater intelligence and flexibility makes them optimal for more complex environments. In fact, according to the Automation Trends Report 2022, businesses utilizing AMR’s have seen a 31% increase in both productivity and efficiency.
At Cyngn, we build self-driving AMRs that can make intelligent, real-time decisions. Our AMRs can be integrated into existing workflows and help build out the routes, loops, and missions that a driver would usually carry out. The increased flexibility and advanced intelligence of our AMR’s allows for greater value, insights, and uptime.
Others Warehouse Robots
In addition to AGVs, AS/RS, and AMRs, there are many other industrial warehouse robots that are equipped with advanced technologies to perform a wide array of tasks like material movement, handling, and logistics operations. These include robotic palletizers, shuttle systems, sortation robots, and goods-to-person systems, all contributing to the optimization of warehouse operations for enhanced efficiency, accuracy, and productivity.
Read More: What are the Differences Between AGVs, AMRs, and AS/RS
Bulk Material Handling Equipment
Engineered systems leverage various technologies to enhance logistics and supply chain efficiency. In contrast, bulk material handling equipment is designed to focus on efficiently managing, storing, and moving large amounts of raw materials. This includes utilizing equipment like conveyors and hoppers tailored for bulk applications.
Conveyors
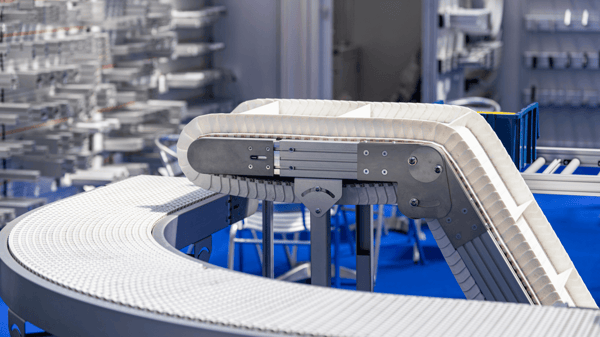
Conveyors efficiently transport large quantities of bulk materials throughout facilities. Whether facilitating a continuous flow on belt conveyors or ensuring controlled transfer on roller conveyors, these machines are designed to handle a diverse range of bulk goods — from raw materials like bulk grains to finished goods such as packaged items — with greater precision and reliability.
Hoppers
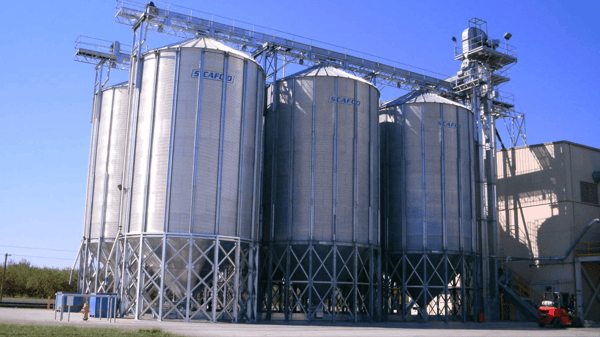
Hoppers are designed to store and guide the flow of bulk materials, ensuring a steady supply of materials. These funnel-shaped containers act as storage units for bulk materials, helping facilitate smooth material flow and making it easier to load downstream processes in a facility. As a result, they play a crucial role in enhancing material flow control and overall efficiency in intralogistics.
Hoppers can accommodate different types of materials, such as grains, powders, or aggregate, and therefore are typically found in various industries from agriculture to manufacturing. In fact, hoppers are often used in conjunction with conveyors or other handling systems.
Industrial Vehicles
In addition to engineered systems and bulk handling equipment, automated forklifts, tuggers, and other specialized machines are commonly utilized to enhance the efficiency and adaptability of material handling systems.
Engineered systems are specialized and technologically advanced solutions designed for specific tasks within industrial automation. On the other hand, industrial vehicles cover a broader category of motorized vehicles that have long been utilized in industrial settings, encompassing both manual and automated versions. As we’ll explore, this includes automated forklifts and automated tuggers.
Automated Forklifts
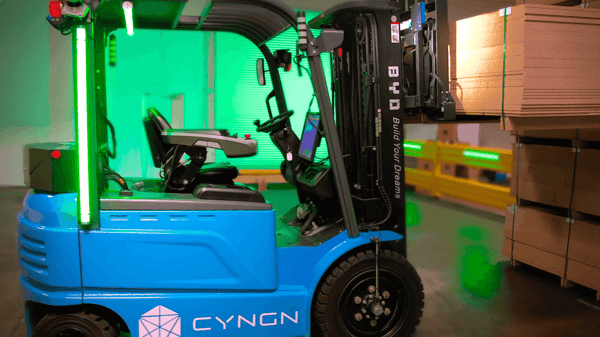
Forklifts are one of the most commonly used industrial vehicles in material handling operations globally. Predictably, automating these worker vehicles is revolutionizing how work gets done and specifically how materials are moved around facilities.
Leveraging cutting-edge technology that utilizes various sensors, cameras, LiDAR, and navigation systems, automated forklifts can autonomously lift, transport, and stack heavy materials without a human operator.
This leads to unmatched precision and a safer working environment, prompting organizations to ramp up their investment in these self-driving vehicles. In fact, according to 360 Market Updates' new survey, the automated forklift market will increase from $3,512 million to around $6,733 million by 2031.
At Cyngn, our DriveMod Forklift uses AI and computer vision to detect and analyze pallet dimensions in real-time, allowing you to handle over 10,000 lbs of material without a human operator. Our vehicles are also equipped with intelligent load stability features so that the forklifts maintain balance and stability when it is operating.
By handling heavy or asymmetrical loads safely and efficiently, these automated forklifts can make a significant impact on how work gets done.
Watch here to see our DriveMod Forklift in action.
Automated Tuggers
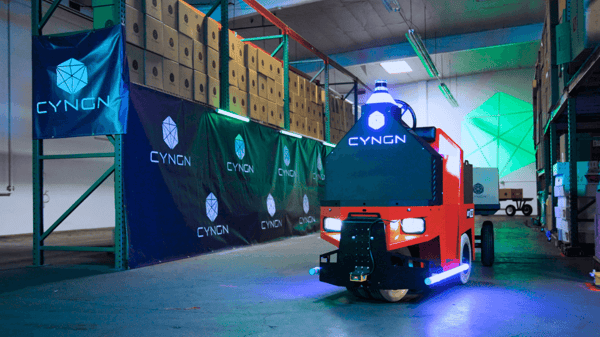
Automated tuggers are designed to efficiently transfer and deliver materials. By automating repetitive tasks and adapting to dynamic environments using real-time data, autonomous tuggers help organizations enhance overall efficiency and adaptability in material handling systems.
Cyngn’s DriveMod Tugger, for instance, uses vision-based navigation to automate repetitive hauling workflows such as transferring finished goods or delivering supplies. These vehicles can tow between 10,000-20,000 pounds, depending on the model, and pull multiple tugger carts. A fully automated tugger train can also reallocate higher-value responsibilities to employees, allowing for higher output.
Explore our autonomous tugger workflows.
Other Industrial Vehicles
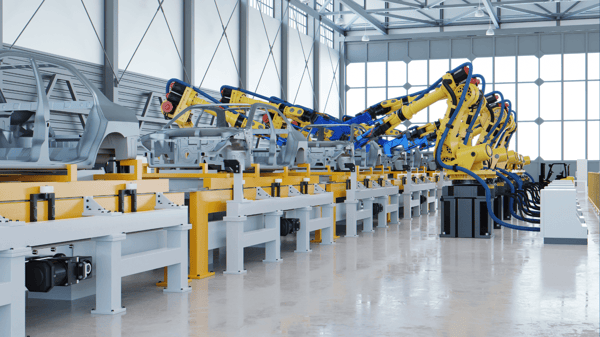
In addition to automated forklifts and tuggers, there are many other industrial machines designed for industrial tasks.
Some examples include:
Automated Tow Tractors: Tow tractors autonomously pull loads and often have tow capacity ranging anywhere from 7,500 to 10,000 pounds, contributing to efficient material transportation in industrial facilities.
Automated Guided Carts: These carts navigate autonomously and can be used for transporting various materials within a facility.
Automated Shuttle Systems: These systems utilize automated vehicles to move and retrieve goods within high-density storage systems.
Automated Conveyor Systems: While not traditional vehicles, conveyor systems play a crucial role in material handling, automating the movement of goods along predefined paths.
10 Principles of Material Handling (MHI)
The 10 principles of material handling are crucial for organizations involved in material handling. As we’ll explore, they serve as guidelines to ensure the full optimization of their MHS. When organizations commit these 10 principals, they increase the throughput and profitability of their organization.
1. Planning
Organizations should work to guide seamless operations through planning. This involves the organization of resources, workflows, and timelines to ensure optimal efficiency throughout the material handling process.
2. Standardization
In order to unify operations, organizations should standardize their processes, equipment, and procedures.
3. Work
Without hindering productivity or output levels, businesses should consider automating their processes to reduce physical strain. For instance, a manufacturing facility might employ automated guided vehicles (AGVs) to transport raw materials directly to production lines, maximizing productivity and limiting physical strain.
4. Ergonomic
Organizations can help reduce physical strain, worker fatigue, and potential injuries by prioritizing ergonomics. In doing so, you can optimize human well-being and system performance.
5. Unit Load
Organizations can optimize unit load by strategically grouping and consolidating materials into a single load to maximize material flow and improve efficiency. For instance, one practical example is palletizing goods before shipping.
6. Space Utilization
Companies can also utilize space strategically by optimizing available space for storage and movement. For instance you can implement vertical storage systems to capitalize on available space without expanding your facility's footprint.
7. System
Organizations can use a coordinated system of various processes, equipment, and people to improve operations. An example may be implementing conveyor systems that connect packaging, sorting, and shipping stations, promoting a continuous and efficient flow of goods.
8. Automation
By adopting automated solutions to enhance speed and accuracy in material handling, organizations can increase productivity and reduce reliance on manual labor.
9. Environment
Material handling systems should be designed with sustainability in mind, which includes adopting safe and sustainable practices. In doing so, organizations can align their material handling practices with broader environmental goals, contributing to long-term ecological sustainability.
10. Life Cycle
Lastly, organizations must consider the total cost of material handling processes such as equipment’s run-time. Companies can use technology, strategic planning, and standardization to develop systems that meet current needs and anticipate future challenges throughout the equipment’s lifespan.
Applications and Uses of Material Handling Systems
3PL
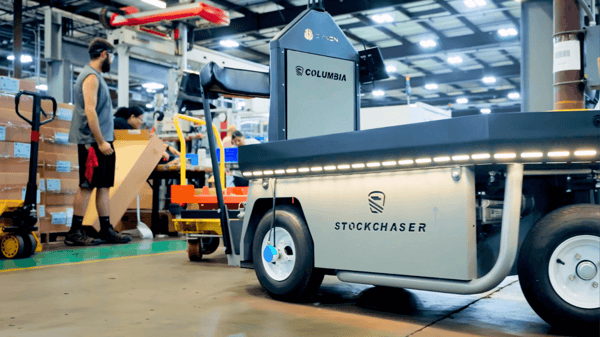
Material handling systems (MHS) are integral to 3PLs by ensuring the swift and secure movement of goods through the supply chain, enhancing efficiency and optimizing storage in supply chain operations. By scaling operations through material handling systems, 3PLs can better meet the changing demands of customers.
For instance, a 3PL firm may deploy MHS systems such as AS/RS, automated conveyor systems, or robotics to streamline their processes. At Global Logistics & Fulfillment, a leading 3PL provider, employees upgraded their pallet transportation efficiency by replacing a manual pallet jack with Cyngn’s autonomous stockchaser. As a result, the organization found a 33% increase in their efficiency within their operations.
Warehousing
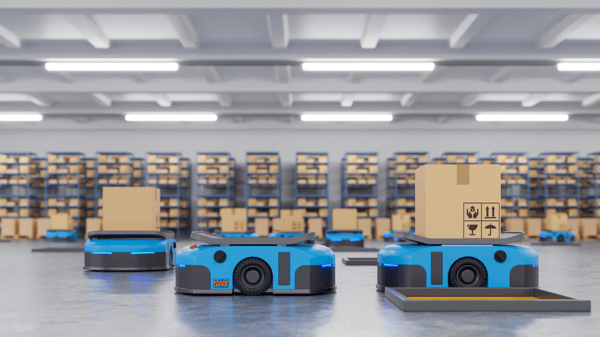
Material handling systems also play a pivotal role in intralogistics within warehouses by overseeing the movement and storage of goods. These systems contribute to the seamless flow of materials, enhancing overall efficiency in warehouse operations.
This includes automating tasks such as inventory management, loading and unloading, order picking, and establishing efficient processes for handling items. Warehouses also leverage MHS to optimize space utilization, ensuring efficient storage and retrieval of goods.
For instance, Walmart plans to redirect 55% of their fulfillment volume through fully automated facilities by 2026, which in turn will reduce the need for manual labor and increase their order processing speed. Other examples of MHS used in warehouses include automated storage and retrieval systems (AS/RS), conveyors, palletizers, and automated forklifts that contribute to more efficient operations and material flow.
Manufacturing
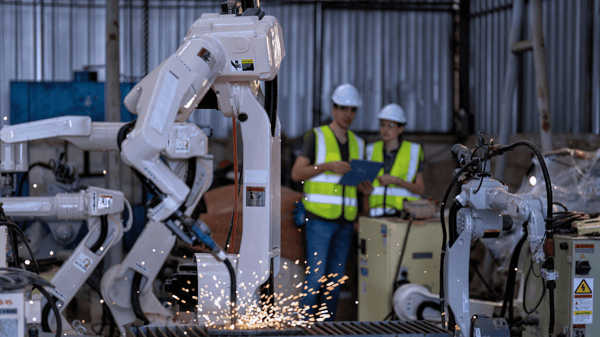
According to Ricoh, around 12% of US manufacturers have integrated robots into their operations, marking a significant shift in how manufacturing work gets done. Manufacturers often use conveyor systems and robotic handling systems to assemble, pick, pack, and sort materials.
For instance, we can look at Flambeau, a manufacturer and distributor of many products, including toys, sporting goods, automotive, and industrial parts. Their decision to deploy one of Cyngn’s AVs not only helped optimize their manufacturing and distribution processes, but also allowed them to re-allocate labor efforts to higher value activities, like converting raw materials into physical products.
Construction
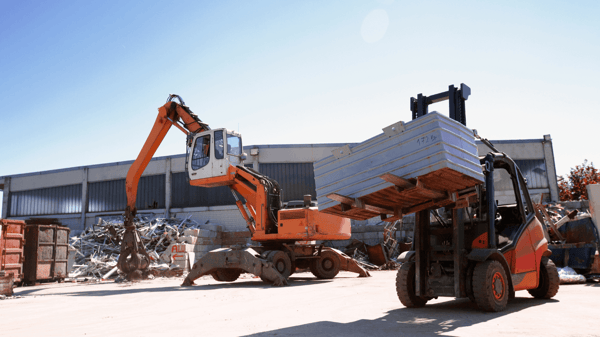
Material handling systems are used to transport and manage construction materials, such as concrete, steel, and aggregates on job sites. Some examples include conveyor systems, cranes, hoists, and material handling robots.
Today, construction companies are implementing automated material handling systems and are already seeing immediate impacts. Caterpillar's semi-autonomous Compact Track Loader utilizes the same robotic technology that powers material handling robots. This allows workers to control up to four machines at once to handle monotonous and repetitive tasks, leaving them the opportunity to work on more engaging tasks.
Distribution
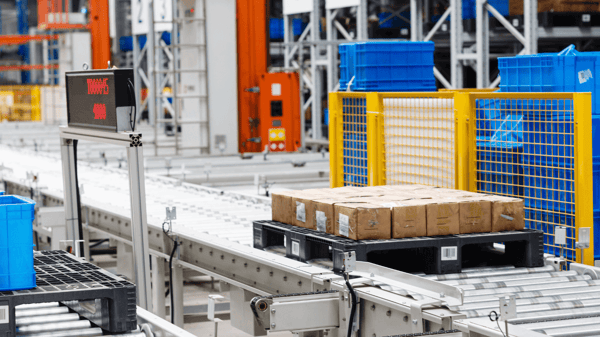
Common MHS systems used by distribution organizations include automated conveyor systems, robotic pickers, and automated guided vehicles (AGVs). These advanced systems are key to optimizing distribution, guaranteeing timely order fulfillment, and significantly enhancing inventory accuracy.
FedEx uses automated sorting systems to efficiently handle large volumes of packages. In addition, they utilize conveyor belts and sorting machines to help organize and route packages based on their destinations, ensuring timely and accurate deliveries.
Leverage Automated Handling in 2024 with Cyngn
One way to leverage automated material handling in 2024 is by incorporating Cyngn’s fleet of self-driving AMRs to do your most demanding industrial jobs. Our AI-powered technology, DriveMod, enables you to automate your workflows in order to minimize safety risks, increase adaptability and accuracy, and boost productivity by 33%.
DriveMod's capabilities extend to a variety of vehicle types such as the BYD Forklift, the Motrec Tugger, and the Columbia Stockchaser. These vehicles can autonomously lift, transfer, and deliver materials so that your workers can focus on more value-adding tasks. Plus, DriveMod gets all of your vehicles humming as a single, unified AV fleet so you can work faster for less.
In addition to replacing monotonous tasks to higher-value tasks for human workers, DriveMod ensures safe, reliable self-driving capabilities, intelligently navigating any space and completing tasks with precision. DriveMod has the ability to:
- Autonomously lift and haul thousands of pounds of goods.
- Switch into manual mode and be driven by a human.
- Safely navigate sites without the need for special infrastructure.
- Transport goods to any on-site location, indoors and outdoors.
- Execute missions based on a variety of flexible, programmable options.
- Collect real-time data to reveal opportunities for optimization.
Frequently Asked Questions