What is Interoperability?
Interoperability in manufacturing is the ability of different industrial systems, equipment, and devices to connect, communicate, and exchange information seamlessly across production processes. It allows hardware and software to support each other, enabling partners, including customers, suppliers, and various departments, to share information quickly and accurately, regardless of their manufacturer or design.
This capability is crucial in today's digitally connected world, as it helps streamline operations, reduce inefficiencies, and improve overall productivity.
The importance of interoperability in manufacturing has grown significantly with the advent of Industry 4.0 and the Industrial Internet of Things (IIoT).
According to an Accenture study, companies with high interoperable systems grew revenue 6X faster than their peers with low interoperability and are set to unlock an additional five percentage points in annual revenue growth.
For instance, Siemens AG, under the leadership of CEO Roland Busch, has been at the forefront of promoting manufacturing interoperability. Their MindSphere platform, an open IoT operating system, has helped numerous manufacturers achieve seamless data exchange between various production line systems, resulting in a 10% increase in overall equipment effectiveness.
According to a study by Accenture, only about 40% of industrial manufacturers have managed to achieve high interoperability. Furthermore, over two-thirds of companies surveyed cited technical complexity as a key barrier to achieving interoperability. These challenges limit the full integration of automated systems and automation processes, slowing the transition to the future of manufacturing.
A Frost & Sullivan report reveals that in the automotive industry, which is considered a leader in adopting connected technologies, only 55% of large and small automotive OEMs and SMEs have started investing in digitizing their plants. This indicates that even in advanced sectors, there's still significant room for improvement in implementing interoperability solutions.
This gap presents a significant opportunity for improvement across the industry. Companies like Rockwell Automation, led by CEO Blake Moret, are addressing this challenge by developing solutions such as the FactoryTalk InnovationSuite, which enables manufacturers to connect disparate systems and achieve greater interoperability, resulting in reported efficiency gains of up to 30% for their clients.
The Role Interoperability Plays in Manufacturing
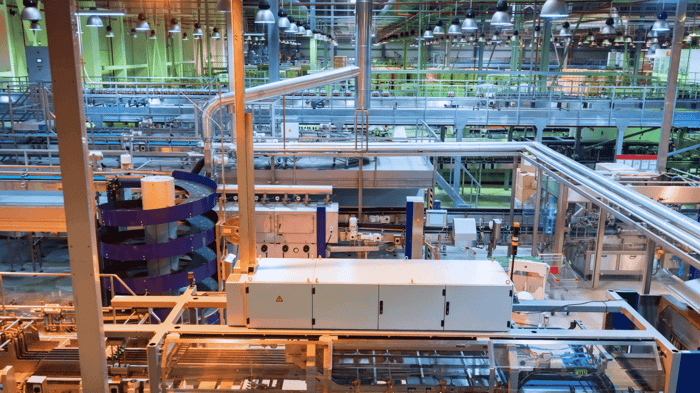
Interoperability plays a crucial role in modern manufacturing as the backbone of Industry 4.0, enabling more efficient, flexible, and data-driven operations. By enabling seamless data sharing and communication between various systems, equipment, and devices, interoperability transforms manufacturing floors into interconnected ecosystems.
This connectivity enhances coordination among assembly lines, reduces downtime, and ultimately boosts productivity. With real-time monitoring capabilities, manufacturers can quickly detect anomalies, make informed decisions, and more effectively optimize supply chains.
Moreover, interoperability bridges the gap between Information Technology (IT) and Operational Technology (OT) systems, enabling the transformation of collected data into actionable insights. This integration empowers workers to perform repetitive tasks like inventory tracking, quality inspections, or equipment monitoring more efficiently, while enhancing security and reliability in decision-making processes.
As manufacturers increasingly adopt Industry 4.0 technologies—such as industrial robots, advanced analytics, and simulation—interoperability becomes essential for harnessing the full potential of these innovations.
Despite challenges such as connecting heterogeneous systems and addressing outdated industrial equipment, the benefits of interoperability are driving manufacturers to prioritize its implementation for improved competitiveness and operational efficiency.
Why Interoperability Matters for the Future of Factories
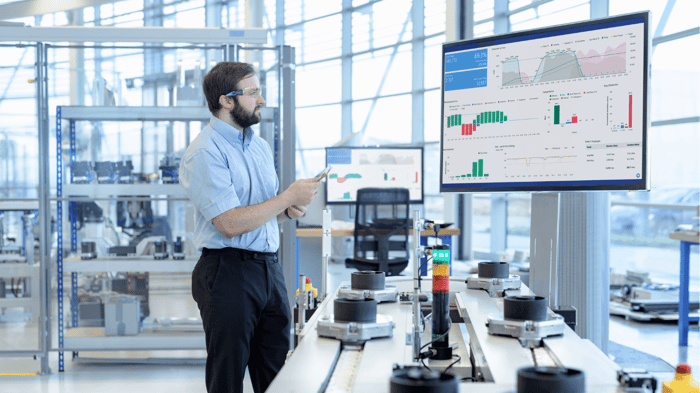
The future of interoperability is crucial for the future of industrial automation, as it enables seamless integration and communication among diverse systems, equipment, and devices.
This capability is essential for unlocking the full potential of Industry 4.0, enabling smarter, more flexible, and more efficient automation in the manufacturing industry. By breaking down silos and enabling real-time data exchange, interoperability enhances coordination between production lines, reduces downtime, and significantly boosts productivity.
In addition, interoperability empowers manufacturers to leverage vast amounts of data generated by IoT devices and sensors, facilitating data-driven insights that inform better business decisions.
With improved analytics and flexible automation, manufacturers can optimize supply chain operations, enhance inventory management, and support demand forecasting. These capabilities are critical to the future of manufacturing as companies adopt advanced technologies like machine learning and programmable automation.
By prioritizing interoperability, factories will be better positioned to adapt to changing market demands, reduce operational costs, and maintain a competitive edge in an increasingly digital industrial landscape.
Manufacturing and Factory Automation Pain Points and Costs
Interoperability plays a crucial role in modern manufacturing as the foundation for Industry 4.0, enabling more efficient, flexible, and data-driven operations.
By facilitating seamless data sharing and communication between various industrial automation systems, equipment, and devices, interoperability transforms manufacturing floors into interconnected ecosystems. This connectivity enhances coordination among production lines and reduces downtime, ultimately boosting productivity.
This efficiency is particularly critical given the staggering costs of unplanned downtime, which are estimated to burden U.S. manufacturers with $50 billion annually. According to a report from Information Technology Intelligence Consulting Research, 98% of organizations report that a single hour of downtime costs over $100,000, with 33% of companies experiencing costs exceeding $1 million per hour.
As a result, major manufacturers are embracing interoperability to optimize their operations.
For instance, Siemens AG has leveraged the OPC UA standard to achieve better coordination between production lines, increasing productivity and reducing downtime. Similarly, General Electric (GE) implemented its Predix platform, which supports open standards like OPC UA, to enable predictive maintenance and streamline supply chains.
The benefits of interoperability are significant, with IDC predicting that organizations sharing data, applications, and operations with their industry ecosystem will enjoy a revenue increase three percentage points higher than those that do not.
However, challenges remain, such as connecting different business process systems and dealing with legacy equipment that may be 20-30 years old and incompatible with modern digital infrastructure. Despite these challenges, the adoption of interoperability continues to grow as manufacturers recognize its potential to enhance operational efficiency and competitiveness in the Industry 4.0 landscape.
The Future of Factory Automation and How Interoperability Solutions Help
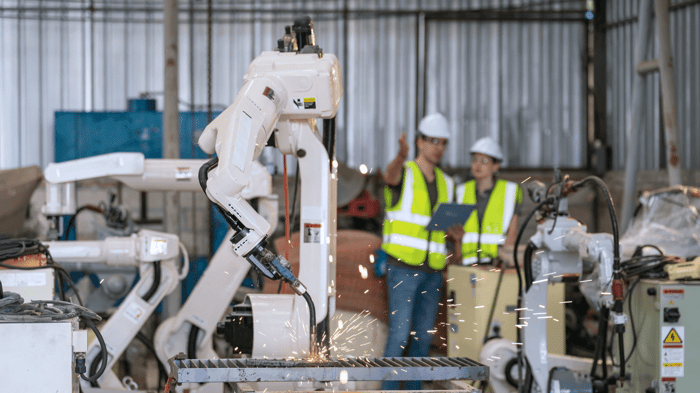
The future of factory automation is set to undergo significant transformation, driven by trends including digitization, the Industrial Internet of Things (IIoT), and the integration of artificial intelligence (AI).
According to a report from Ericsson's Industry Lab, 70% of manufacturers expect to deploy at least five ICT-enabled production tools within the next five years. These tools enable real-time data collection and analysis, improving efficiency across industrial processing operations
Additionally, the global industrial automation and control systems market is projected to grow at a compound annual growth rate (CAGR) of 10.8% from 2025 to 2030, driven by the integration of automated systems and industrial robots. Robotics is also playing a pivotal role in evolving fixed automation processes into more dynamic and scalable systems.
For instance, companies like Amazon, under the leadership of CEO Andy Jassy, are at the forefront of warehouse automation. Amazon's substantial investments in robotics, with more than 750,000 robots deployed across their facilities worldwide, and AI-driven systems illustrate how automation can revolutionize large-scale operations.
However, the transition to fully automated manufacturing presents challenges; nearly two-thirds of manufacturers anticipate being automated to at least 80% within ten years, but there remains a disconnect regarding workforce implications.
How Cyngn’s Autonomous Solutions are Ready to Meet the Future of Interoperability
%20(1).png?width=700&height=394&name=Article%20Images%20-%202025%20(1)%20(1).png)
At Cyngn, we prioritize interoperability to ensure our autonomous solutions integrate seamlessly with the systems you already rely on. Our open architecture and API support give you the flexibility to customize integrations that meet your unique operational needs.
Our fleet management system enables real-time monitoring and coordination, ensuring smooth communication across platforms. With teleoperation capabilities built in, we ensure continuous and adaptable operation, even in the most complex environments.
Ready to future-proof your operations? Reach out today to see how Cyngn’s interoperable solutions can drive efficiency and scalability for your business.
Frequently Asked Questions